Summary
Our laboratory aims to research "digital manufacturing systems" based on mechatronics, automation and digital technology, working from a broad perspective from design design and prototyping to CNC machine tools, industrial robots, automated transport, sustainable production systems and process elucidation. Toward the IoT and information society synchronized with the development of computers, technological innovations such as machine learning and AI (artificial intelligence) are also actively introduced into our systems. We are also engaged in research and development related to technologies for a sustainable society that takes into account the cooperation between humans and machines and the global environmental impact that will be necessary for the next generation of manufacturing (manufacturers). While "the importance of manufacturing is universal," it is believed that "the technology of how to make things is constantly changing. Toward the needs of a changing society, we will promote research and development of autonomous, distributed, and cooperative "making," "manipulating," and "transporting" based on globally applicable mechatronics technology.
Poster
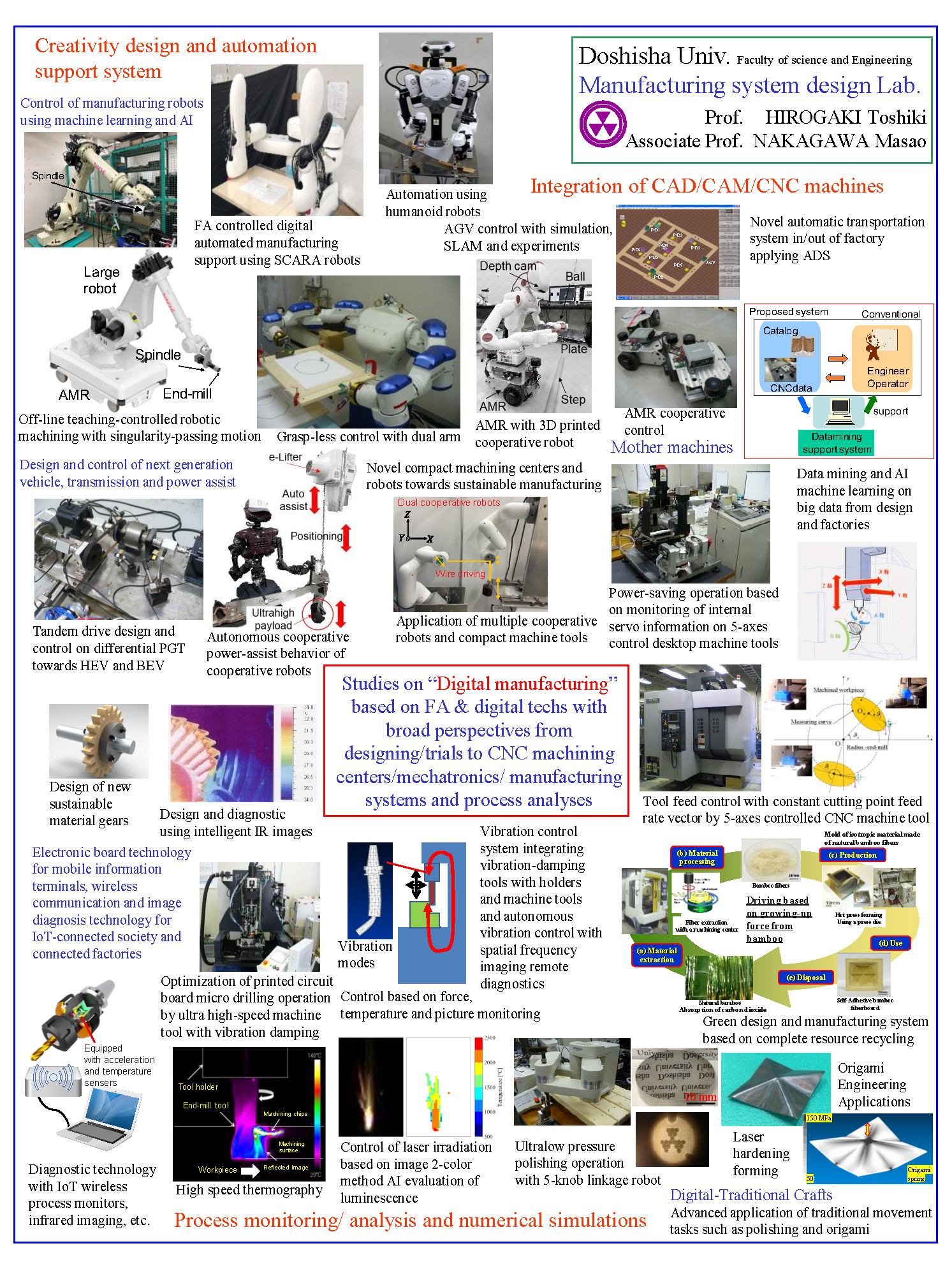
Machine tool related
- Study on tool approach and various shape generation under a constant cutting point feed speed vector control on 5-axis controlled machining center (Otsuki)
- Study on cutting mark control in two-blade ball-nose end mill machining based on combined motion of linear axis and swivel axis of 5-axis controlled machining center (Yoshimura)
- Barrel and lens tools on 5-axis controlled machining center Wireless toolholder force monitoring and pattern image processing for cutting mark pattern control (Sugiura)
- Study on inverse analysis state monitor using two-dimensional discrete Fourier transform images of machining surface patterns and chips in end mill chatter vibration of machine tools (Konno)
- A Study on Thread Milling Based on Monitoring of a Wireless Tool Holder and Servo Date in Machine tool, and the Evaluation of Thread Functional (Matsunoshita, Tanaka)
- Motion Analysis of a Compact Five-Axis Machine Tool with Harmonic Drives for Warm-Up Operation and Energy-Efficient High-Precision Performance (Iwashita, Tanaka)
- Study on new power saving processing method that no idling multi-tasking machine tools combine turning and straight movement (Imai)
- Study on differences in machining path motion of multi-tasking machine tools with idling stop, power saving and higher accuracy, and evaluation of actual machined surfaces (Tada)
- A new small number of tooth gears of condition monitoring during end mill machining by 4-axis controlled machining center and performance analysis (Yang)
- Examination of high-speed step motion of an ultra-small-diameter drill on a machine tool equipped with an ultra-high-speed spindle with counter dynamic balance mechanism (Yuuki)
- Study on helical movement during hole milling CFRP for aircraft with electroplated barrel endmill based on servo information, force and strain monitoring (Shirai)
- CAD/CAM technologies based on integrated machine tools control and sensing information (Ghatas, Tanaka)
Robot
- Development of drilling and end milling technology and improvement of accuracy of CFRP for off-line teaching of large industrial robots (Kanzaki)
- Investigation of drill processing under passing through wrist singularity conditions based on offline teaching with a large-scale industrial robot (Uchino)
- Investigation of motion accuracy under two-axis plate rotary motion control with an industrial dual-arm robot using gyroscopic sensor (Hatanaka)
- Investigation of grasp-less handling of shaking agitation in in-plane maneuvering motion of the work plate of a twin-arm scalar robot (Yamashita)
- Study on motion accuracy of working plate operation for grasp-less manipulation with dual-arm SCARA robot (Wada)
- Low-Impact Object Placement via Cooperative Wired-Driving with Articulated Robots (Tsubaki)
- Investigation of a placement method based on the evaluation of a new coordination in wire-driving movements using two compact cooperative robots (Tsujioka)
- Study on power-assisted cooperative motion and advanced manipulation of electronic musical instruments by dual-arm cooperative motion with a 3D printed asymmetric humanoid robot (Kashiwagi)
- Study on Sound Feedback Motion of Advanced Musical Saw by Dual-Arm Coordination of Humanoid Robot (Liu)
- Study on Advanced Musical Saw Manipulation Motion and Power Assist by Dual Arm Coordination for Humanoid Robot (Santa)
- Investigation of Sound Feedback Control of Advanced Denim Shaving Motion by Dual Arm Coordination of Humanoid Robots (Kawata)
- Plate manipulation for grasp-less ball handing for FA with a humanoid robot under its moving conditions(Wu)
- Study on Task Motions of a 3D-Printed Humanoid Robot While Transporting Objects over Steps (Oikawa)
- Ultrasonic assisted polishing operation of five-bar planar parallel robot by controlling polishing force (Tong)
Gear
- Investigation of drive control method during step shifting in three-axis differential planetary gear train under tandem drive based on high-speed video monitoring (Mitsuishi)
- Investigation of drive control method during frequency response repeatedly shifting speed in three-axis differential planetary gear train under tandem drive based on high-speed video monitoring (Tange)
- Investigation of the Influence of planetary gear tooth surface accuracy on vibration and noise during gear shifting in three-axis differential planetary gear train under tandem drive conditions (Ma)
- Elucidation of one-tooth pinion high-ratio hypoid gears meshing phenomenon using high-speed video infrared thermography monitor and heat transfer model (Takeuchi)
- Study on the Influence of Temperature Rise during Engagement of Oil Content on the Tooth Surface of High Ratio Hypoid Gears Using Infrared Thermography and Airbrush Lubricant Supply Control Method (Onozeki)
Bamboo material
- Study on the tensile fracture mechanism of fine bamboo fiber thermocompression molded products extracted using a machining center (Nakahara, Tanaka)
- Analysis of meshing of environmentally friendly bamboo fiber bevel gear and face gear by monitoring tooth vibration and tooth root strain and its application to design (Murata)
Data mining
- Study on the discovery of new knowledge in barrel tool catalog information by introducing AI and machine learning methods for data mining (Hou)
- Discovering new knowledge in microdrill catalog information by introducing AI machine learning methods in data mining (Chitose)
- Analysis of end mill catalog information using AI machine learning techniques in data mining and application to lens tools (Oyaizu)
AMR
- Development of AMR that can adapt to various environments and study on various cooperative work with humans by AMR (Omi)
- Investigation of advanced factory operations by integrating SLAM and ROS2 robots in a complex environment of Autonomous Mobile Robot (AGVs and AMRs) (Sasa, Omi)
- Examination of mechanism and control method for overcoming large steps under SLAM in an indoor factory of an automated guided vehicle (AGV/AMR) (Oishi, Omi)
- Development and application of AGV at outdoor (Long, Omi)
Laser processing
- Construction of a laser irradiation control system for via-hole based on two-color method video image AI monitor for digital twin (Morishita, Fujimoto)
- Application of Origami Engineering in Laser Quenching Forming Process Examination of Complex Plate Spring Shapes with Support Surfaces (Uranishi, Fujimoto)